Unprecedented demand, rapid market expansion and limited future resources mean OEMs need to urgently prepare for operating in a highly competitive future.
In under 20 years, Tesla has gone from a start-up to the most valuable automotive OEM in history and now every other legacy car manufacture is playing catch up. In order to compete, companies are rapidly developing their own EV product lines with a hope to try and retain market share in the electric future. This changing landscape has created new companies, with the sole focus on developing and producing batteries on a “giga” scale to keep up with projected demand. But without a collaborative approach to development from OEMs, mining companies and recycling facilities, all this development may be in vain if predicted bottlenecks in raw material supply and sustainability concerns become a reality. OEMs need to start to pre-emptively be two steps ahead of known future issues and urgently need to consider a wider holistic view of what intelligent technology and sustainable business plans will be required to underpin their automotive future.
Unsustainable supply chains look to be the next major bottleneck in the electric transition.
Volatility and shortages in supply of key materials like Lithium, Nickle and Cobalt is the major point of concern with the rapid transition to EVs. Currently, OEMs have the capabilities to make electric vehicles, but if battery materials are not produced at a comparable rate, then the just-in-time supply chain that underpins the industry could grind to a halt. The European Commission predicts these key materials to be in deficit as early as 2025, highlighting the importance of ensuring a robust supply chain and sustainable sourcing of raw materials. Already stretched due to limited supply, accelerated iterative battery design and chemistry developments will soon create significant shortages in upstream battery production. The automotive industry therefore needs to transition to more collaborative supplier relationships, allowing for flexible sourcing to mitigate fluctuations in demand caused by changes in battery design.
Cross-value chain approach to vehicle design is a necessity to create an optimised circular economy.
Not only will future battery technology changes have an impact on upstream supply chains, but they will also have a knock-on impact throughout the battery’s future lifecycle. Sustainable design engineering needs to be at the forefront of battery and EV design, with an emphasis on designing with circularity in mind as illustrated in Figure 1 (below). Recycling companies are looking to address EV circularity issues with leaders in the industry such as Glencore, Veolia & Redwood Materials expanding facilities to handle the surge of degraded EV battery packs that require disposal. But to improve the level of circularity within this ecosystem required to reach their claimed 95% recycling rate of key materials, a more collaborative approach to battery pack design is required.
At present, the sector is highly dispersed in its battery designs and charging strategies. Some companies such as NIO are concentrating on battery swaps, with their competitors like Tesla investing in fast charging. Others like Momentum Dynamics have diverged completely and are focusing on developing wireless charging technology. This makes the sector feel almost reminiscent of the handheld tech industry in the mid-2000s, with a multitude of charging cables and old batteries now confined to the bottom kitchen drawer. But unlike the tech of old, these pieces of tech won’t quite fit in a drawer and serious thought needs to be taken around the circular design of batteries, what ownership model OEMs will deploy and will they look to retain the precious metals in the cells that will be in short supply in the future. OEMs can overcome this by adapting their operating models to make strategic decisions around the level of vertical integration across the vehicle value chain, forming key strategic partnerships with recyclers, logistics companies and battery producers. Companies will have to collaborate at pace using agile principles to develop new products using whole lifecycle assessment tools, ensuring downstream and upstream activities are not impacted, but optimised for retention of product value.
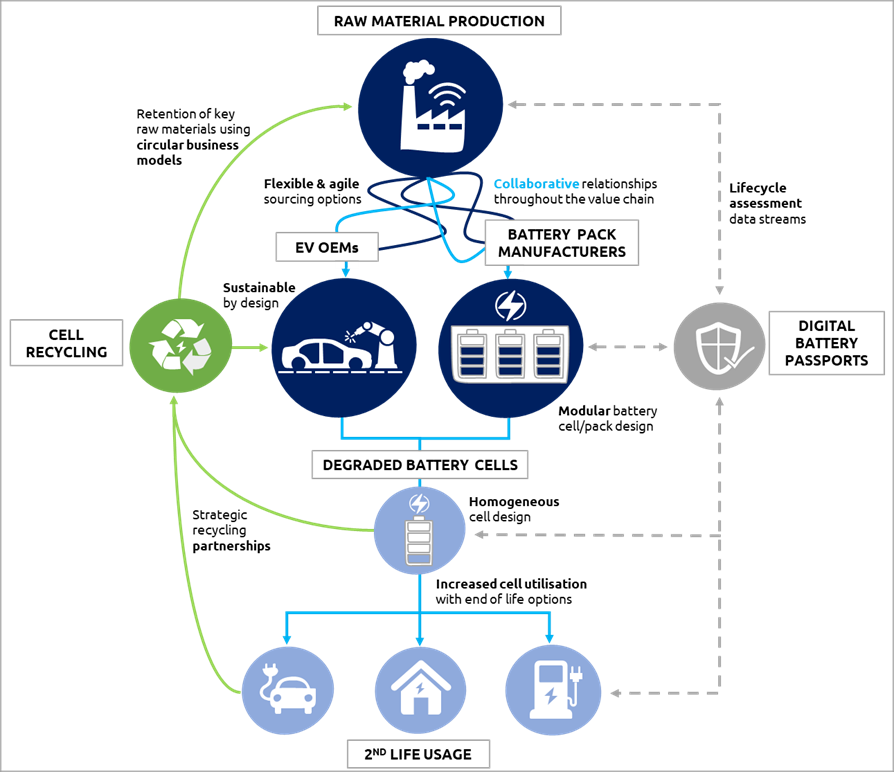